Scott MacDonald’s Exquisitely Beautiful ‘True’ Custom Guitars
Ask Scott MacDonald why he quit a successful career in TV and film production some 24 years ago to start his guitar shop – building and repairing guitars – he offers a simple explanation.
“It was an inner voice that said this is what you should be doing. I have no other answer,” he explains.
Actually, the inspiration to transform rough wood into exquisite musical instruments most likely took root when he built a banjo as a college student. Then later, while working in the film business, he built a guitar from a kit.
He laughs, “It didn’t explode when I put the strings on. That’s when I first heard the voice.”
Surprisingly, MacDonald never studied guitar making or apprenticed with a master luthier. He simply attended some workshops and symposiums where he asked questions and listened to guitar makers.
“I always knew I could call on people smarter than I if needed. After that, it was just time and experience learning my craft,” he says.
Today, MacDonald operates a successful business building and repairing guitars and other musical instruments from his shop in Chester, VT. His client list includes customers from around the globe.
Every guitar he makes is one-of-a-kind. String lengths, fretboard marking, all dimensions and choices of wood are worked out for each individual. No two are alike.
“Everything is designed around the guitar player. When I get to know the person, the guitar comes out of that. I study the size of the customer’s hands, the tone of their voice, how they play. The finished product is a true custom guitar that fits them like a glove,” he says.
Stable, Good Sounding Wood
MacDonald works with a variety of sustainable wood species, avoiding all endangered species. All are stored and crafted in his 4-zone humidity-controlled workshop.
“I look for wood that’s going to be stable, sound well, and make a great instrument.”
He’s learned to tell how good a piece of wood will sound simply by scratching it, tapping on it, and seeing how it feels in his hands. He says it’s an intuitive thing that came with time.
Beauty is another factor. “I look for wood that’s aesthetically lovely, but it also has to meet all the criteria of making a great instrument.”
Before working on a piece of wood, he stores it for six to 12 months in his humidity-controlled shop. As he explains, “It’s just to make sure that it’s really happy where it is.”
Moisture Content Critical
Humor aside, MacDonald says he can’t build a guitar unless the wood is ready for him to build it. That means controlling the relative humidity (RH) and checking the wood for moisture content (MC).
To keep tabs on the RH, he uses an Abbeon Certified Hygrometer. As the RH fluctuates, he controls it by humidifying and dehumidifying his shop to keep it at the ideal range.
“The relative humidity is vital. I like it to be in the 47% to 50% range. And the wood must be between 6% to 8% MC,” he says.
To make certain the wood is indeed ready to be worked, MacDonald always uses a Wagner pinless moisture meter. He avoids pin meters because they make unsightly holes in the wood and they don’t give him accurate moisture readings deep in the wood or across a wide area.
“The two-pronged meter might be good for someone building a house, but when you’re building handmade custom guitars – where the moisture level is absolutely critical – you need an accurate reading. If I get inaccurate readings, my guitars would become unstable.”
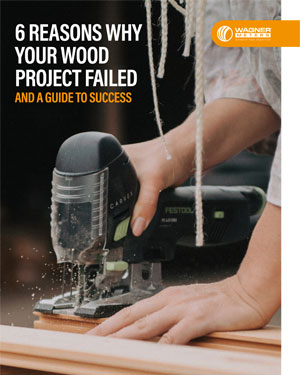
Free Download – 6 Reasons Your Wood Project Failed
As a luthier, MacDonald believes he’s only as good as his environment, his materials, and his tools. “That’s why I keep my shop humidity-controlled year-round, buy the finest materials, and why I bought the Wagner MMC220 moisture meter. It was the best moisture meter I could find,” he declares.
“And trust me, I’ve tested it against other cheaper brands and the readings weren’t even close. They weren’t close because with those other meters you can’t select the specific gravity or species of the wood. If you put a meter on a piece of pine and then you put it on a piece of ebony, that’s like comparing balsa wood to steel.”
“The size of the pores and the ability of the wood to take in and release moisture can be staggeringly different between species. So you can’t just put a meter on a piece of wood and know precisely what the MC is. With the Wagner, I can dial in a specific species – whether it’s ebony, maple, or spruce – and know I’m going to get an accurate reading,” he says.
A True Artist’s Passion
Talk to MacDonald and in short order you know he’s passionate about making guitars. You soon sense his love of transforming rough wood, as if by some form of alchemy, into beautiful, vibrant instruments – each with its own individual characteristics and personality.
Anyone who has ever played a true handcrafted custom guitar from S.B. MacDonald Custom Instruments knows it can “sing” in sweet, rich, lovely sounds, and become a “voice” for the player. To learn more about MacDonald’s work, go to www.customguitars.com.
To choose a wood moisture meter that’s right for your projects, visit https://www.wagnermeters.com/moisture-meters/comparison-matrix/.

Wagner Meters is a family-owned American business that aims to provide solutions in moisture measurement technology that will enhance the quality and value of each customer’s project. With an almost 60-year legacy of innovation, Wagner continues to be a resource for both individual craftsmen and high-performance commercial endeavors.
Last updated on May 4th, 2021